Quantas vezes, na hora de sair de casa, já atrasado, você perdeu ainda mais tempo a procura de sua carteira, da chave de casa ou do carro? Por que isto acontece? É evidente que este problema é causado por desordem, acúmulo de coisas que não são mais utilizadas, falta de um local apropriado para guardar suas coisas.
Fazendo uma comparação com uma linha de produção, pense em um funcionário da manutenção que não encontra rapidamente a ferramenta que necessita para ajustar uma máquina. Assim como no exemplo de sua vida pessoal, este problema certamente se deve às mesmas causas que listamos anteriormente. No caso do ambiente fabril, esta perda de tempo gera a espera do equipamento, causando por consequência uma redução de produtividade e o aumento dos custos unitários de produção.
Trabalhar em ambientes limpos, com iluminação adequada, com níveis de ruído dentro das normas aumenta a autoestima do funcionário e, consequentemente, a sua produtividade. Hoje falaremos sobre o 5S, uma filosofia que permite manter seu ambiente de trabalho limpo e organizado.
História do 5S
No Japão de 1950, as fábricas eram sujas, desorganizadas, barulhentas, escuras e a produtividade e a qualidade eram baixas. Precisando criar diferenciais de mercado, deixando de ser apenas um “copiador” de produtos, o Japão precisava mudar esta história. E é ai que entra os 5S, uma filosofia simples, mas muito poderosa e que deve ser a base para qualquer programa de qualidade. Em outras palavras, é por esta filosofia que devemos começar. Impossível, ou muito difícil, seria implantar um sistema de gestão da qualidade (SGQ) sem antes implantar a filosofia dos 5S.
Os 5S passaram a ser incorporados à cultura japonesa, sendo atualmente passados de pai para filho e nas escolas, não se restringindo apenas à utilização em ambientes de trabalho.
Um vez, indagaram a Kaoru Ishikawa: “Por onde começar um programa de gestão da qualidade numa empresa?” O professor Ishikawa respondeu prontamente: “Comece varrendo a fábrica!”,
“Como assim, professor Ishikawa?”, indagou o interlocutor, completando: “O senhor quer dizer que devemos varrer a empresa, retirando quem não tem competência ou apresenta baixo desempenho?”
Ad
Então, Ishikawa explicou que varrer a fábrica significava retirar a sujeira do chão, limpando os espaços, deixando as coisas organizadas, gerando um ambiente propício a que as pessoas pensem, procurem, e pratiquem boas maneiras de fazer as coisas.
Conceito de 5S
Os 5S são um programa de gestão da qualidade desenvolvido no Japão, na década de 1950, que visa aperfeiçoar aspectos como organização, limpeza e padronização. Mas porque se chama 5S? Seu nome 5S vem de cinco palavras japonesas que começam com S: seiri, seiton, seiso, seiketso e shitsuke. No Brasil, chamamos estes “S” de sensos (de arrumação, ordem, limpeza, padrão e disciplina).
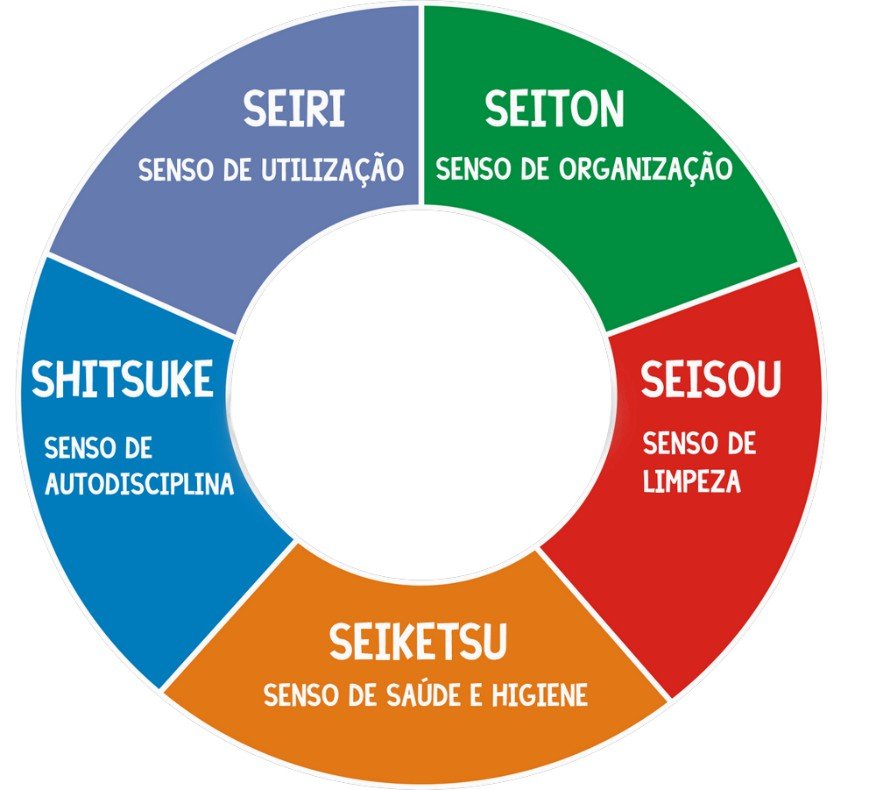
Seiri
Este é o nosso primeiro S. No Brasil, traduzimos como senso de utilização ou senso de arrumação. Você se lembra de quando falamos em acúmulo de coisas em casa que poderiam lhe atrapalhar para encontrar as chaves do carro? Chegou a hora de resolvermos este problema. Este senso nos ajuda a separar o que é necessário do que é desnecessário.
No ponto de vista do ambiente de trabalho, o seiri consiste em analisar os locais de trabalho e classificar todos os itens (objetos, materiais, informações, etc.), segundo critérios de utilidade ou frequência de uso, para depois retirar do ambiente tudo o que não precisa estar ali
Repare que “tudo que não precisa estar ali” é um conjunto muito amplo que não envolve somente equipamentos quebrados. Podem existir materiais e equipamentos perfeitos para o uso que, por alguma razão, não são mais utilizados.
Ad
Outro detalhe importante é a classificação dos materiais mesmo dentro daqueles que ainda são considerados necessários. Tenha em mente que não temos como mantê-los todos no posto de trabalho, assim precisamos priorizá-los. Podemos classificá-los em três tipos:
a) Utilização imediata: estes devem ficar no posto de trabalho. Por exemplo, uma ferramenta para ajuste constante da máquina.
b) Utilização rotineira: estes não são utilizados com a mesma frequência. Assim, podem ficar um pouco mais afastados.
c) Utilização esporádica: estes podem passar dias sem ser utilizados.
Por esta razão, podem ser guardados ainda mais distantes do posto de trabalho. Desta forma, com o início do senso de utilização, começam a surgir os materiais inúteis, que devem ser removidos para uma “área de descarte”. Nessa área, todo o seu material deve ser devidamente identificado. A
área de descarte não é sinônimo de bagunça, até porque, nesta área, há muita coisa que pode ser útil para outro setor ou pode ser vendida. Por isso, o descarte deve estar organizado e os objetos de fácil localização.
Nesta etapa, é importante analisar e separar o necessário do desnecessário, eliminar ferramentas, armários, prateleiras e materiais em excesso ou fora de uso e eliminar dados de controle ultrapassados, por exemplo.
Como benefício esperado, há a diminuição do desperdício e o aumento de espaço para trabalhar com aquilo que realmente agrega valor à atividade do setor, trazendo à tona as suas reais necessidades de melhoria.
Ad
Aplicando Seiri
PREPARAÇÃO
• Identificar ONDE cada tarefa do seu processo é executada.
• Cuidar para que cada tarefa seja executada em local adequado e preparado para tal.
• Discutir com as pessoas envolvidas.
• Identificar cada item do mobiliário, relacionando-os.
• Incluir na relação o número do patrimônio, se houver.
• Avaliar a real necessidade de tê-los. Mantenha apenas o necessário e justificável no local de trabalho.
Ad
• Relacionar todos os dispositivos.
• Verificar a utilização dos dispositivos, isto é, por que existem, a frequência de uso, quantas pessoas os utilizam, etc.
• Relacionar todos os documentos existentes e utilizados.
• Verificar a utilização dos documentos, isto é, por que existem, por que estão ali, qual a utilidade deles, a frequência de uso, quantas pessoas os utilizam, etc.
• Relacionar a matéria-prima existente e consumida na área.
• Verificar a aplicação e o consumo.
• Verificar a necessidade de existência de estoque.
IMPLANTAÇÃO
Ad
• Definir um layout (disposição de mobiliário) que seja funcional e seguro. Funcional se refere à disposição em que o fluxo de trabalho se desenvolve, sem ocasionar perda de tempo. Segura é aquela disposição em que a movimentação de pessoas, materiais e equipamentos é desimpedida de obstáculos.
• Colocar os excessos à disposição de outras pessoas.
• Promover a venda ou sucateamento do inservível.
• Providenciar a reposição daquilo que estiver faltando.
• Para repor ou adicionar mobiliário, aproveite o descarte das outras áreas e pessoas, em primeiro lugar.
• Eliminar a multiplicidade de documentos.
• Descartar os papéis desatualizados e que não sejam úteis.
• Antes de descartar documentos, verifique se não existe legislação específica que determina a necessidade de mantê-los em arquivo.
Ad
• Definir o destino de cada grupo de documentos.
• Definir o período de permanência de cada grupo de documentos no seu devido local e indicar quem será o responsável por sua atualização.
• Adequar os estoques às necessidades de consumo de cada item relacionado.
• Acompanhar os consumos e custos de estoques no sentido de
reduzi-los gradativamente.
MANUTENÇÃO
• Preparar uma planta com as dimensões básicas e disposição dos
móveis, dispositivos e equipamentos. Esta planta servirá como
Ad
base para que sejam mantidas as mudanças realizadas e para
as auditorias.
• Elaborar um procedimento que oriente as alterações que se fizerem necessárias no futuro.
Definir quem, quando e como os itens de consumo serão repostos (plano de reposição).
• Elaborar procedimentos que orientem a inclusão/exclusão de dispositivos e a localização deles no arranjo geral.
• Definir vida útil, no caso de ferramentas de desgaste, e estabelecer procedimentos de reposição.
• Elaborar procedimentos que orientem a inclusão/exclusão de dispositivos e a localização deles no arranjo geral.
• Estabelecer formas de controle de consumo para construir um histórico e ajustar níveis de consumo.
Ad
• Definir nível mínimo e máximo de estoque para cada item de consumo.
Seiton
Agora que já separamos o material que realmente é necessário daqueles que podem ser descartados, chegou a hora de organizar, arrumar o espaço de trabalho.
O objetivo aqui é facilitar que os materiais sejam encontrados, evitando assim a perda de tempo. Imagine uma grande fábrica onde não haja um lugar definido para se guardar as ferramentas de uso diário. A cada vez que estas fossem solicitadas, haveria perda de tempo. Logo, você precisa fazer o seguinte:
1. O primeiro passo é definir o local em que os materiais devem ser armazenados. Para isso, podemos usar a dica do primeiro “S”, quando falamos da utilização imediata, rotineira e esporádica. Assim, os materiais do primeiro grupo devem ser armazenados mais próximos dos locais onde serão demandados e assim por diante.
2. Aplique rótulos e etiquetas nas prateleiras e armários, para assim identificar quais ferramentas são guardadas ali. Isso facilitará o acesso, o armazenamento e os inventários.
3. Etiquete e rotule também as ferramentas. Isso ajudará o trabalhador a saber onde a ferramenta deverá ser guardada após o uso.
A figura a seguir mostra a aplicação do seiton em uma oficina mecânica. Veja que o quadro de ferramentas já vem desenhado com a figura das ferramentas no lugar correto em que estas devem ser guardadas.
Ad
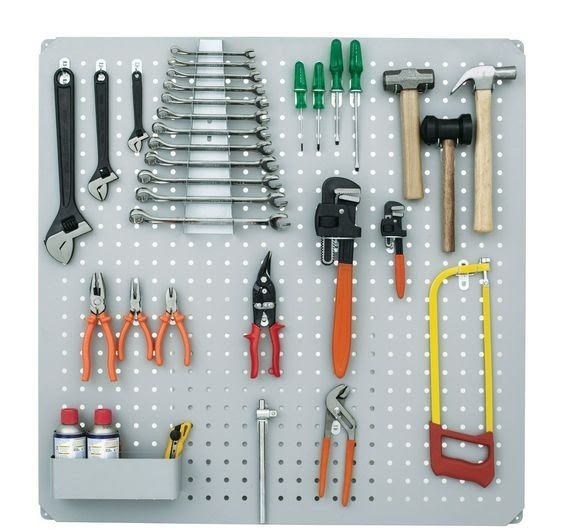
Você certamente já pratica o seiton sem saber. Por acaso, você não cria pastas em seu computador para separas arquivos por categorias? Pois é, você está aplicando o seiton. Aqui buscamos:
• definir um lugar para cada coisa e alocar cada coisa em seu lugar;
• guardar objetos semelhantes/afins no mesmo lugar;
• aproveitar todos os espaços de forma inteligente, evitando deixar espaços vazios;
• definir o layout com foco no melhor fluxo, demarcando-o e sinalizando-o;
• identificar e sinalizar tudo de maneira coerente e visível, facilitando ao máximo a busca e respeitando as regras da nossa gramática.
Sabemos que, em ambiente organizado, tudo se encontra com rapidez e facilidade: documentos, materiais, ferramentas e outros objetos. Não se perde tempo e diminui o desperdício de recursos, minimizam-se os erros e aumenta a produtividade. Este é o benefício do seiton!
Ad
Aplicando Seiton
PREPARAÇÃO
• Padronizar os nomes dos dispositivos.
• Agrupar por tipo, natureza, função ou aplicação.
• Discutir amplamente com as pessoas envolvidas a melhor maneira de ordenar, os locais de guarda e a melhor forma de acondicionamento.
IMPLANTAÇÃO
•Colocar em prática a forma de ordenação definida, incluindo a guarda e o acondicionamento.
• Sinalizar os locais indicando os grupos, subgrupos e itens.
Ad
• Ordenar por tamanho e em ordem sequencial.
• Educar os usuários para utilizarem corretamente os padrões adotados.
MANUTENÇÃO
• Elaborar uma folha de verificação periódica para garantir a ordenação permanente.
• Definir os responsáveis pela verificação, a frequência e preparar estas pessoas para isto.
Seiso
Nosso terceiro S, o seiso, foi traduzido como senso de limpeza. Não se trata apenas de limpar, mas sim de manter um ambiente sempre limpo. Pense bem, esta talvez seja a parte mais difícil! Arrumar seu quarto um dia pode ser fácil, mas mantê-lo sempre arrumado é um passo adiante. É disso que estamos tratando no seiso.
Aqui, há uma quebra de paradigma, pois a limpeza deve deixar de ser vista como uma tarefa da equipe de limpeza e passar a ser incorporada no trabalho de todos os funcionários. Ou seja, o próprio operador de equipamentos é responsável por parte da limpeza de seu posto de trabalho.
Ad
Ao se manter em excelentes condições de limpeza o ambiente de trabalho e os equipamentos, contribui-se para o bem-estar e a segurança de todos, bem como para o aumento de produtividade. Aqui vale a máxima: MELHOR DO QUE LIMPAR É NÃO SUJAR! Procure:
• descobrir e eliminar as fontes de sujeira;
• educar e definir procedimentos para não sujar;
• limpar tudo o que utilizar logo após o seu uso;
• conservar limpas mesas, gavetas, armários e equipamentos em geral
Assim, com a melhora o ambiente de trabalho, o nível de segurança e a satisfação dos colaboradores por trabalharem em um ambiente limpo aumentarão.
Aplicando Seiso
PREPARAÇÃO
Ad
• Identificar as formas de sujeira.
• Planejar ações para eliminar os efeitos (limpar).
• Identificar as causas e fontes de sujeira.
• Planejar ações para eliminar as fontes e as causas identificadas.
IMPLANTAÇÃO
• Implantar as ações de bloqueio definidas no plano de ação e verificar a sua efetividade.
MANUTENÇÃO
• Criar procedimentos envolvendo as ações de bloqueio que se mostraram eficazes na remoção das causas de sujeira.
Ad
• Preparar as pessoas para seguir os procedimentos.
Seiketsu
O quarto S foi traduzido como senso de padronização, higiene e saúde. Ele visa padronizar comportamentos trazendo conforto para a saúde física e mental dos colaboradores.
Após termos estudado as três primeiras etapas do programa 5S, devemos partir para a padronização e melhoria contínua das atividades. Essa etapa exige perseverança, pois se
não houver mudanças no comportamento das pessoas e nas rotinas que geram sujeira, logo voltaremos à situação inicial, antes da implantação do 5S.
Assim, com o seiketsu, conseguimos manter a organização, arrumação e limpeza obtidas através dos três primeiros S (seiri, seiton, seiso).
Além do ambiente de trabalho, o asseio pessoal acaba melhorando, pois os funcionários, não querendo destoar do ambiente limpo e agradável, acabam por incorporar hábitos mais sadios quanto à aparência e a higiene pessoais.
Nessa etapa, devem ser elaboradas normas para detalhar as atividades do 5S que serão executadas no dia a dia e as responsabilidades de cada um. Com a padronização, qualquer coisa que fuja dos 5S fica evidente para qualquer colaborador, o qual passa a refletir e mudar antigos hábitos, melhorando a sua forma de trabalhar de acordo com o que vê acontecer ao seu redor.
Ad
Aplicando Seiketsu
PREPARAÇÃO
• Identificar fatores de risco no ambiente de trabalho.
• Identificar as fontes e possíveis efeitos nocivos às pessoas.
• Identificar os cargos expostos a cada risco.
• Identificar o número de pessoas expostas e o tempo médio de exposição para cada risco.
• Medir os valores dos fatores de risco.
• Identificar a necessidade de EPI/EPC.
Ad
• Identificar as causas e elaborar um plano de ação para bloqueio de causas, eliminação das fontes de risco ou atenuação dos seus efeitos.
IMPLANTAÇÃO
• Adotar medidas para atenuar os efeitos ou eliminar os riscos.
• Elaborar procedimentos para ação em emergências.
• Medir os riscos após ação de bloqueio e avaliar melhoria.
• Atualizar o mapeamento de risco da área de trabalho
MANUTENÇÃO
• Certifique-se que os procedimentos sejam do conhecimento de todos.
Ad
• Simule situações de emergência periodicamente, como forma de treinamento.
• Institua um sistema de verificação periódica do cumprimento dos padrões.
Shitsuke
Agora que passamos pelas quatro primeiras fases, ou os quatro primeiros S, arrisco dizer que teremos pela frente o mais difícil deles: o shitsuke, que é traduzido como autodisciplina. Em outras palavras, quero dizer que mais difícil do que arrumar e organizar o ambiente de trabalho é mantê-lo desta forma. Assim, os ganhos obtidos nas fases anteriores devem ser mantidos.
Quantas vezes já organizamos nosso local de trabalho, ou até mesmo nosso quarto, e dias depois a mesma bagunça já estava novamente instalada?
As exigências naturais deste senso são:
• compromisso dos envolvidos: para isso todos precisam entender os benefícios e seus papeis no programa 5S.
• educação, paciência e responsabilidade;
Ad
• respeito às normas estabelecidas;
• comunicação das metas e dos resultados obtidos: isto ajuda a manter os funcionários
motivados e consequentemente envolvidos no programa 5s.
De uma forma geral, este senso aumenta a disciplina, ao passo que as pessoas passam a fazer o que tem de ser feito e da maneira como deve ser feito, mesmo que ninguém esteja olhando, passando assim a viver de fato a filosofia da melhoria contínua.
Aplicando Shitsuke
PREPARAÇÃO
• Criar uma folha de verificação de não conformidades, baseada nos quatro primeiros sensos.
• Estabelecer uma frequência de avaliação das áreas a serem submetidas ao quinto senso.
Ad
• Definir um calendário de avaliação.
• Definir um critério para a formação dos grupos de avaliação (auditores).
IMPLANTAÇÃO
• Seguir criteriosamente o programa de avaliação.
• Utilizar o PDCA para resolver os problemas identificados.
• Utilizar um gráfico de controle para acompanhamento.
• Utilizar o relatório de não conformidades observadas para alavancar melhorias.
MANUTENÇÃO
Ad
• Alterar os padrões e os procedimentos tão logo tenha sido identificada a causa fundamental dos problemas.
• Divulgar amplamente os novos padrões.
• Promover o treinamento das pessoas
Exemplos de 5S aplicados em fábricas
O vídeo abaixo é um bom exemplo de como a Toyota aplica 5S.
5S sendo aplicado em uma fábrica
Ad
Vale a pena ver esta aula também de 5S:
— Comentários0
Seja o primeiro a comentar